Electro-Slag Furnace
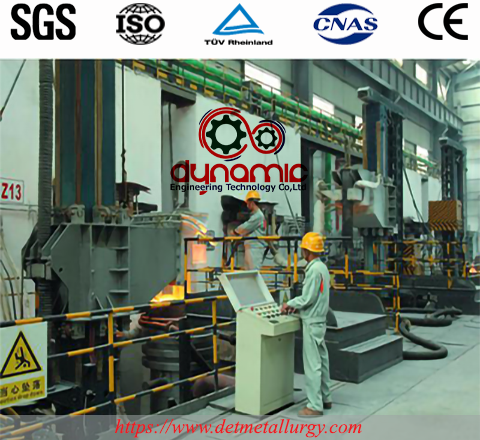
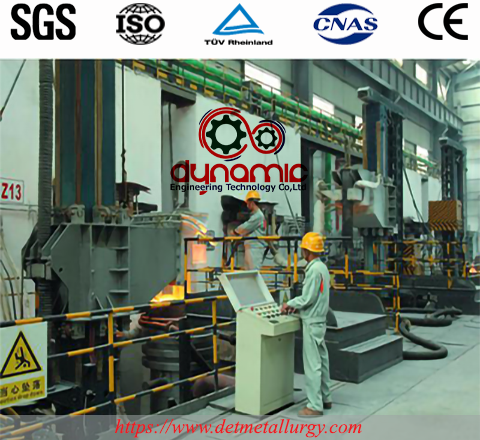
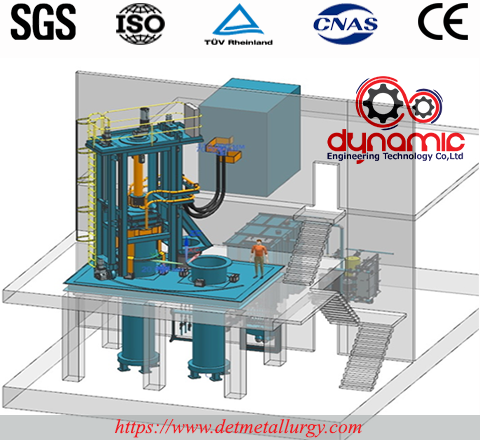
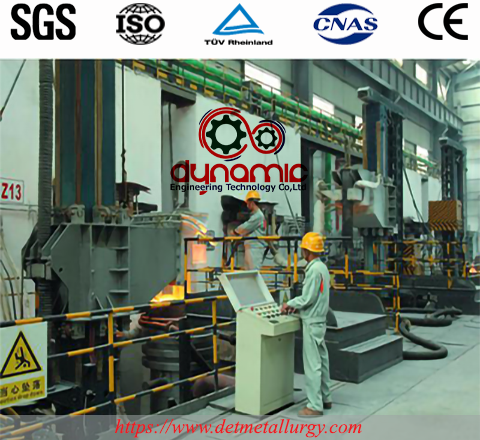
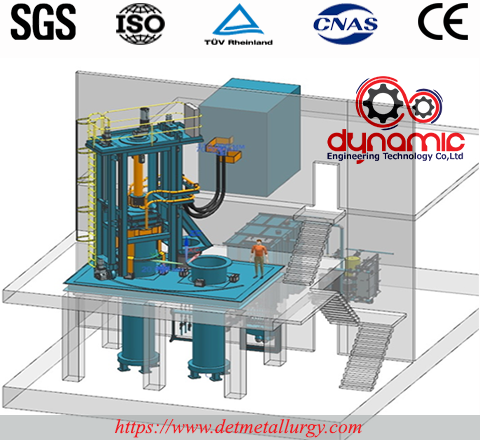
The ESR process involves the gradual melting of the lower end of a cast or forged electrode through a layer of molten metallurgically active slag into a water-cooled copper mold. The slag is usually calcium fluoride with the addition of lime, magnesia, and other oxides. In its molten state the slag is electrically conductive and acts like a resistance heating element when a high current is passed between the electrode and the mold.
With the continued passage of the electric current, the slag becomes superheated. The electrode tip is immersed in this superheated slag and begins to melt. The immersion of the electrode in the slag is precisely maintained and a controlled melt rate is established. An advanced computer control system maintains the melt rate and electrode
immersion utilizing custom designed algorithms taking into account measurements from the load beam weighing system, measurements of the furnace voltage (or resistance); and control of the power supply current.
The molten metal droplets sink through the lower density molten slag and re-solidify in the water-cooled copper mold. Through this process the slagmetal reactions dissolve inclusions and purify the metal as it falls through the molten slag.